How Did Colour Coded Cleaning Come About?
The British Institute of Cleaning Science (BICSc), back in the 1990’s was the first institution to develop a universal colour code standard, and although it is not enforced by law this code has been adopted across the Hospitals, Aged Care, Professional Institutions as well as the cleaning industry at large, because of its health and environmental benefits.
The BICSc has, over the years has reviewed its code and aligned it with those from other organisations such as the National Patient Safety Agency. The BICSc believes all cleaning equipment and materials within a hospital janitorial store area should be colour coded, cleaning products like cloths, buckets, mops and aprons etc, it is a common belief this reduces the risk of cross contamination in the varied cleaning environments.
What is Colour Coded Cleaning and Cross Contamination?
Colour coded cleaning was created to reduce the risk of cross contamination when cleaning. It is the process of applying colours to cleaning cloths and cleaning equipment in areas of a venue, reducing the spread of germs across various areas and increasing hygiene standards throughout commercial or domestic environments. The main colours being, blue, green, red and yellow are used to separate areas such as washrooms, bars, public areas, food preparation areas and kitchens.
The Food Standards Australian New Zealand (FSANZ) suggests that separate colour coded cloths and cleaning equipment should be used in areas where food is handled, prepared, and eaten.
Where health and safety are paramount, colour coding is used throughout, particularly in healthcare and catering as cross contamination can lead to an unsafe workplace and serious illness. Colour coded cleaning cloth and cleaning equipment colours are representative to their area of use. As an example, you would not want to be cleaning a kitchen food preparation area with a cloth that has been used in a bathroom. The colour coded cleaning areas are broken down in four areas, these being:
- Restaurant and bars – including café lounge and dining area
- Public areas – Receptions, lobbies and hallways
- Kitchen and food preparation areas – food preparation areas, all kitchens and where food is stored or prepared
- Washroom and toilets – including bathrooms, powder rooms and shower areas

WHERE TO USE COLOUR CODED CLEANING CLOTHS AND CLEANING EQUIPMENT?
Colour Coded cleaning products – what colour goes where
The colour coding of cleaning cloths and cleaning equipment has been known to vary from business to business and any system you adopt is entirely up to each business. However, the previously mentioned guide is the most universally accepted, currently used by most catering and healthcare establishments and institutions in their cleaning process. Any colour coded cleaning process you choose will rely on your staff members understanding and being trained to understand what you decide as your colours. There are, however, regulations for healthcare that must be followed to ensure patient care.
Businesses are advised to follow the guidelines set out by FSANZ and in particularly Standard 3.2.3.(See below). The use of colour coded cleaning cloths and cleaning equipment has been particularly useful having been widely adopted by catering, retail, factories and offices. FSANZ outline the importance of maintaining a high degree of food quality, safety and hygiene issues and ensures working environments remain hygienic, healthy and safe. Encouraging colour coded cleaning practices will ensure your workplace benefits from improved productivity and remains safe, efficient and clean.
FSANZ Standard 3.2.3. sets out requirements for the design and construction of food premises, fixtures, fittings, equipment and food transport vehicles. The objective of this standard is to ensure that, where possible, the layout of the premises to minimise opportunities for food contamination. If complied with, these requirements will help food businesses meet the food safety requirements of Standard 3.2.2.
Some exemptions apply to temporary food businesses and businesses operating from a private home. For further information you should contact your state or territory health department or local council.
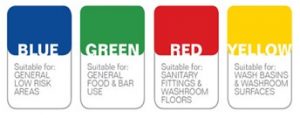
COLOUR CODING CLEANING CLOTHS – ARE THERE OTHER COLOURS IN THE STANDARD?
To avoid cross contamination in other areas outside the four areas already discussed, there are two additional colours bringing the list to 6 colours and where applicable these should be included as part of your normal cleaning practices.
The additional colours are white and brown.
White is used in the healthcare sector in operating theatres and the brown is used in the café sector as a Barista’s colour coded cleaning cloth.
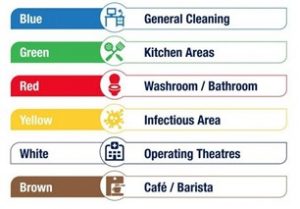
IS COLOUR CODED CLEANING TRAINING NEEDED?
Using a single cloth in every room in a workplace as an example, can potentially spread bacteria from the bathroom to the kitchen. A failure in cleaning practices and hygiene standards can potentially increase the risk of cross contamination possibly leading to the spread of serious illness. When colour coded cleaning cloths and cleaning equipment are used to separate work areas, they significantly reduced the risk of cross contamination. It is therefore even more important to continue to educate and train new staff in the way colour coded cleaning operates in the workplace, and continuous improvement will lead to better productivity.
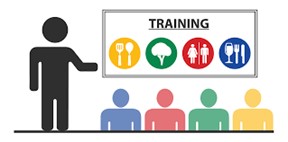
Contact Us
For more information on colour coding in Australia and the products we offer please feel free to contact trugrade via phone or email us any questions you may have.